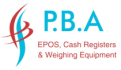
Tel: 01684 290629
email: info@pbaservice.co.uk
PBA
EPOS & Weighing Equipment
Why it is important to maintain Scale Calibration
For many industries, a reliable and accurate industrial scale is at the heart of everyday operations. From weighing large pallets in a shipyard to counting nuts and bolts in a factory, for packing fruit and vegetables to weighing meat and other goods, potential uses for industrial weighing scales vary widely and offer a variety of benefits. Because of their importance, you really need to look after your devices and provide a regular scale care routine to ensure optimal performance. One of the most fundamental ways to do this is to calibrate your industrial weighing scales to ensure a high accuracy.
Why do you need to calibrate a scale?
Scale calibration is essential to providing accurate weighing. results with every use. Working with an industrial scale that has not been correctly calibrated is ill-advised and can cost time and money, as well as potentially impacting your business’ reputation. Reduced quality of your goods or product recalls are just two potentially harmful results that can stem from having non-calibrated weighing equipment.
Over time your scale will lose accuracy – it happens! General day-to-day use combined with inevitable mishaps such as spillages or knocks eventually take their toll. Luckily, setting up a calibration schedule for your scales and balances will increase their longevity and ensure that they remain accurate for longer.
Benefits of calibration
Having correctly calibrated industrial scales ensures that your equipment is ready to go and accurate at all times. Here are eight reasons why calibration is so crucial:
- Accuracy - Sustaining a high level of accuracy for all weight measurements. Obvious, but completely fundamental for all industries that rely on weighing equipment. This could be anything from accurate parts counting to recipe-based industries such as food production or industrial mixing processes.
- Avoiding legal issues - Potential legal issues could arise from incorrectly weighed produce, including anything from customer complaints all the way to fines or even legal action. Many different legal processes must be adhered to, such as using trade approved scales when selling a product based on its weight, or complying with shipping regulations.
- Customer confidence - It is obviously essential that your customers know exactly what to expect and having a calibrated industrial scale or balance helps guarantee that you maintain a strong level of customer confidence.
- Save money - The correct calibration of a balance or scale for industrial use helps to avoid potential issues that could cost money, such as product recalls or wastage. It may also help bypass any shipping and transit issues that could occur as a result of a box or pallet being incorrectly weighed.
- Keep track of aging equipment - Identify any signs of deteriorating equipment. Keeping a regular calibration routine for your scales or balances allows you to spot any signs that they are aging. You are then able to make an informed decision to either repair or replace your instrument.
- Compatibility and uniformity - If you use more than one industrial weighing scale or balance, you will want them to provide the exact same results to avoid inaccurate data and confusion.
- Safety – Your products or produce must remain safe to use for customers. It’s as simple as that. For food production, it could be putting too much salt into a mixture as a result of poorly calibrated scales and breaches food safety guidelines. In industrial mixing such as concrete production, too much or too little of an ingredient could cause the solution to be overly brittle or soft. Safety is an issue that may come in a number of different forms depending on your industry, so you should be up to date with relevant health and safety regulations.
- Save time - Time is always of the essence for any business, so it’s crucial that your industrial scales are ready to go and accurate. If they are not, you risk product recalls or having your produce reweighed whilst in transit.
How often should weighing scales be calibrated?
Generally it depends on the use of the scales, the environment, the frequency of use and the if the scales are moved around, but for the British Retail Consortium (BRC) and Trading Standards it is recommended that scales are calibrated annually, with a calibration certificate issued, detailing the date of the calibration, the results and any action required to rectify any issues. It is also recommended that the scale calibration is checked and recorded before use, so for a food preparation or packaging facility it would be a daily procedure. If the scales are moved from place to place or are in a harsh environment, it is best practice to check the calibration after moving the device. For laboratory balances, with high accuracy, it is always best practice to check on a regular basis, as things like temperature changes, moisture or even a breeze can affect the calibration of the device.